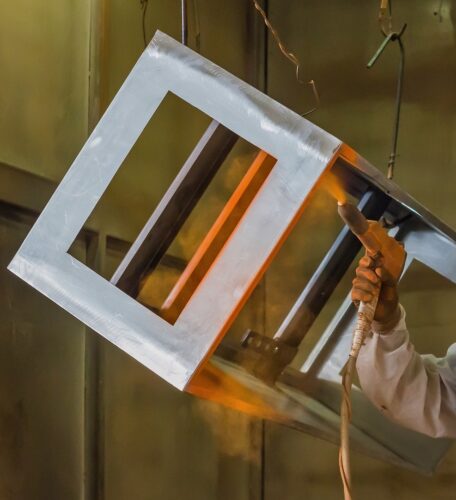
A Guide to Steel Finishing Options
As the final step in many light fabrication and manufacturing processes, steel finishing serves various structural and decorative purposes. It is the last chance to clean, strengthen, or add specific resistances and other desired characteristics to steel and help extend its service life. This post examines some of the most popular steel finish types and the different metal finishing processes that can be used for various applications.
Deburring
Deburring involves the removal of any excess material, ridge, or imperfection that may remain on steel parts following fabrication. It is a prerequisite for other metal finishing techniques, such as powder coating or electroplating, and it is a valuable step in improving a product’s functional and aesthetic qualities.
Shearing, welding, laser cutting, and other machining processes may leave undesirable raised edges or burrs that can interfere with the proper functions, aesthetics, or safe handling of the steel. For smaller parts of certain metals, including carbon steel and stainless steel, thermal deburring uses a flash of heat to vaporize metal burrs quickly. In more-common vibratory or centrifugal barrel finishing for heavier deburring, parts are placed inside a chamber with specially formulated media, including abrasives or water and other compounds. The friction between the media and parts from vibrations or centrifugal force removes the burrs and creates a superior surface finish.
Depending on the application requirements, deburring can be accomplished through wet or dry processes. Wet methods thoroughly polish surfaces and remove excess material, but dry deburring finishing is best for delicate parts and surfaces.
Surface Grinding
In one of the most popular types of finishing methods, steel grinders use abrasive wheels or belts to smooth out the surface of the metal. Often the final step in the steel fabrication process, surface grinding removes or reduces the oxide layer, impurities, and any roughness left over from other machining efforts.
Shot Blasting or Media Blasting
An aggressive and abrasive metal finishing technique, shot blasting is highly effective at cleaning, descaling, roughening, and preparing the steel’s surface for painting or other finishes. Under high pressure, a steady stream of small metal projectiles are propelled against the surface. Shot (and media) blasting removes scales or other surface debris without damaging the underlying steel and provides desired surface preparation with no harsh chemicals or other potentially hazardous materials.
The shot pellets, or media, can range in size and material, with pieces as small as 1 millimeter providing a smoother, more polished look and larger sizes (typically up to 6 millimeters) producing a rougher finish.
Wet Painting
In addition to achieving desired aesthetic effects, water- or oil-based paints provide steel with a cost-effective coating of protection against corrosion. Different paint formulations may be needed depending on the steel’s operating environment or performance requirements.
Galvanizing
The galvanization finishing process involves coating steel with a layer of zinc to protect against rust and corrosive elements. Galvanized steel is popular for various metal fabrication applications, offering enhanced strength, durability, and formability.
It’s a fast, cost-effective process for permanent corrosion protection and requires no ongoing upkeep for enduring strength and appearance. In hot-dipped galvanizing, steel is immersed in molten zinc at temperatures near 450 degrees celsius. For thinner coatings, electroplating galvanizing uses a zinc and salt solution to electrolytically deposit a layer of zinc on cleaned steel surfaces.
Powder Coating
Powder coatings are renowned for their durability and an aesthetically-pleasing appearance.
Steel powder coating gives the metal a decorative finish similar to wet paints but with increased durability. The process can produce a textured, glossy, or matte metal finish using UV or heat curing of a dry polymer powder and an electric charge to attract the powder particles to the surface. Textured powder coat finishes are particularly effective at masking any surface defects.
Passivation
Passivation creates a thin oxide surface film layer to protect the metal against rusting and chemical reactivity.
Passivation protects the underlying iron from rusting by augmenting and optimizing the formation of the chromium oxide layer. An acid bath in either nitric or citric acid dissolves free iron from steel’s surface. The process leaves behind a uniform surface with a higher proportion of chromium than the underlying material for a non-reactive surface protected against rust.
Zinc Plating
Using chemical baths and an electric current, a thin layer of zinc is applied to coat the steel’s surface. On galvanized metal, zinc plating acts as a sacrificial anode and corrodes itself to protect the integrity of the underlying steel.
Zinc plating is typically best suited for large batches of small parts such as screws, nuts, bolts, and other hardware or fasteners.
Heat Treating
Once a part or product’s final shape is attained, heat treatment is essential for adding desirable characteristics to the steel. Various heat treating processes include hardening, tempering, annealing, and normalizing.
Hardening improves the strength of steel by increasing the resistance of its internal lattice structure. The process involves heating the metal to temperatures between 800 and 1,000 degrees celsius before it’s rapidly cooled in a quenching medium of water, oil, or brine.
Following hardening, steel is often more rigid than necessary and could be too brittle for effective manufacturing. Tempering relieves internal stress formed during the rapid cooling process, heating steel before allowing it to cool in still air.
Annealing reduces steel’s hardness and increases its elasticity, making the metal more suitable for various manufacturing processes and applications. The annealing process heats steel beyond its recrystallization point, causing atoms to redistribute and form new grains that make the metal more formable.
Normalizing removes internal stress for parts that need maximum toughness and stress resistance or will be subject to frequent impact, and it leaves steel harder and stronger than annealing.
Metal Finishing with Westfield Steel
For specialty coatings and metal surface finishing methods to serve wide-ranging part specifications or project requirements, Westfield Steel has you covered. Between our in-house capabilities and external partners, we’ll add value via the perfect finish for your steel parts, plates, tubes, bars, and more. Talk to our steel experts today to learn more or receive a no-obligation quote for your steel finishing needs.
Back