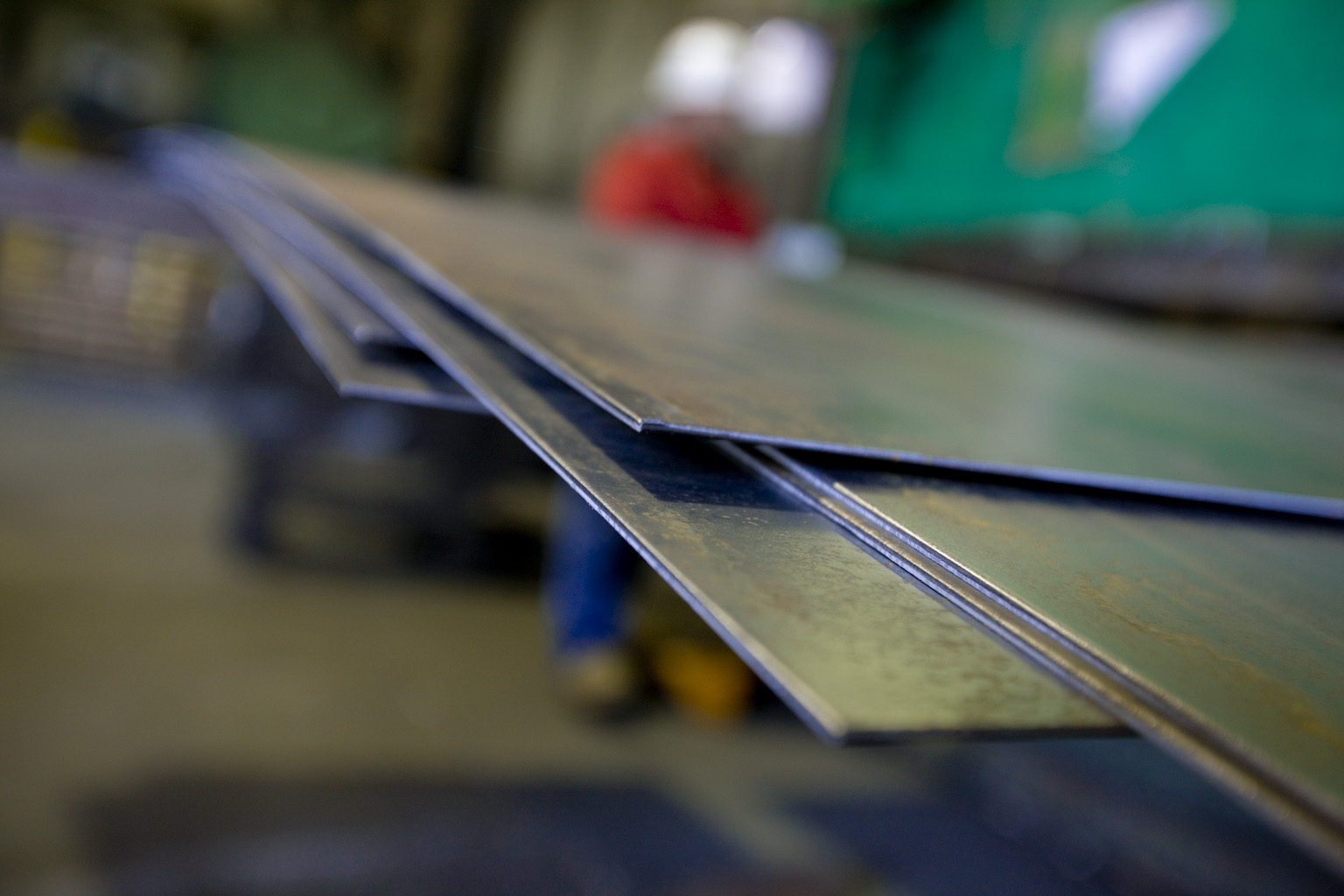
Precision in Structural Steel and Plate Fabrication: Choosing the Right Cutting Method
When shaping steel plates into pressure vessel tanks, heavy machinery, skyscrapers, and industrial components, the chosen cutting method significantly impacts cost, accuracy, efficiency, and final product quality. The three primary techniques—plasma, laser, and oxy-fuel cutting—each offer distinct advantages based on steel plate thickness, edge quality requirements, and production efficiency. Selecting the right cutting process ensures the best balance of precision, speed, and cost-effectiveness.
Making the Cut: How Plasma, Laser, and Oxy-Fuel Methods Work
The choice of a steel plate cutting method is not just about the final results. The way each process interacts with structural steel plates is essential to consider. Understanding the mechanics behind plasma, laser, and oxy-fuel cutting may impact your selection of products or projects.
Plasma Cutting: High-Speed Thermal Precision
Plasma cutting utilizes a superheated, electrically conductive gas to create a high-energy arc that melts through steel plates. The electrically conductive plasma arc is generated between an electrode and the steel plate, and a high-velocity gas stream blows away the molten material to form a clean cut. Plasma cutting is effective for conductive metals, such as carbon steel and stainless steel, and is a common practice for mid-thickness steel plates.
Laser Cutting: High Accuracy with Minimal Heat Distortion
Laser cutting employs a focused beam of light to generate intense heat that vaporizes or melts steel plates along a programmed path. A high-pressure gas stream assists in removing the molten metal, ensuring precise and intricate cuts. Laser cutting is particularly beneficial for detailed designs and high-tolerance applications, as it minimizes heat-affected zones and material distortion.
Oxy-Fuel Cutting: Power Through Heavy Steel
Oxy-fuel cutting or flame cutting relies on a gas and oxygen mixture to heat steel to its ignition temperature. A jet of pure oxygen initiates an exothermic reaction once the metal reaches its ignition point, burning through the steel plate and producing an oxidized slag that is blown away. This powerful cutting method is best suited for thicker steel plates, which often cause plasma and laser cutters to struggle.
Choosing the Right Method Based on Steel Thickness and Edge Quality and Precision
Selecting the appropriate cutting method depends heavily on the thickness of the steel plates. Oxy-fuel cutting is the only option powerful enough to effectively cut through thicker steel plates, making it the popular and preferred choice for heavy-duty fabrication applications.
Laser cutting’s highly focused light beam and minimal material distortion from limited heat spread make it ideal for the thinnest of steel plates under 1 inch. Plasma cutting most often offers a balancing middle ground of speed and accuracy with mid-range thicknesses between ¼ inch and 2 inches.
Edge quality and precision are key to structural integrity, ease of assembly, welding efficiency, and overall product performance. If your project requires steel plates with smooth, precise edges, laser cutting is ideal. It minimizes the need for additional finishing or machining efforts and provides an almost-polished finish.
Plasma cutting also produces steel plates with relatively clean edges but may require minor grinding for high-tolerance applications. Oxy-fuel cutting results in rougher edges, often necessitating further processing to remove slag and achieve a smooth finish.
Production Speed, Efficiency Stats, & Costs Considerations
Production speed is essential for many fabrication projects. Plasma cutting is the fastest option for mid-thickness steel, making it the preferred choice for high-volume fabrication. Laser cutting is slower than plasma for thicker materials, but its precision minimizes the need for secondary processing, ultimately saving time in the finishing stages. Oxy-fuel cutting is the slowest, but it remains the most efficient choice for thick plates, where other methods are impractical.
Cost efficiency varies depending on the method. Plasma cutting provides a cost-effective balance of speed and quality, making it an affordable and practical choice for many structural steel fabrication projects. Laser cutting has higher initial costs due to needing highly specialized equipment, but its precision helps minimize material waste and secondary finishing expenses. Oxy-fuel cutting is the most economical choice for thick steel, as the equipment and operational costs remain relatively low.
Comparing Cutting Methods
See the chart below for a quick reference guide to which primary cutting method is recommended for your steel plate project.
Westfield Steel: Your Partner in Precision Steel Plate Cutting
Westfield Steel brings decades of experience in structural steel and plate fabrication to the cutting table. Whether your products and projects require high-speed production, intricate detailing, or heavy-duty plate cutting, we have the plasma, laser, and oxy-fuel expertise and cutting-edge equipment to do the job right.
Ready to get started? Talk to Westfield Steel’s experts today to learn more about our capabilities and request a personalized quote.
Back