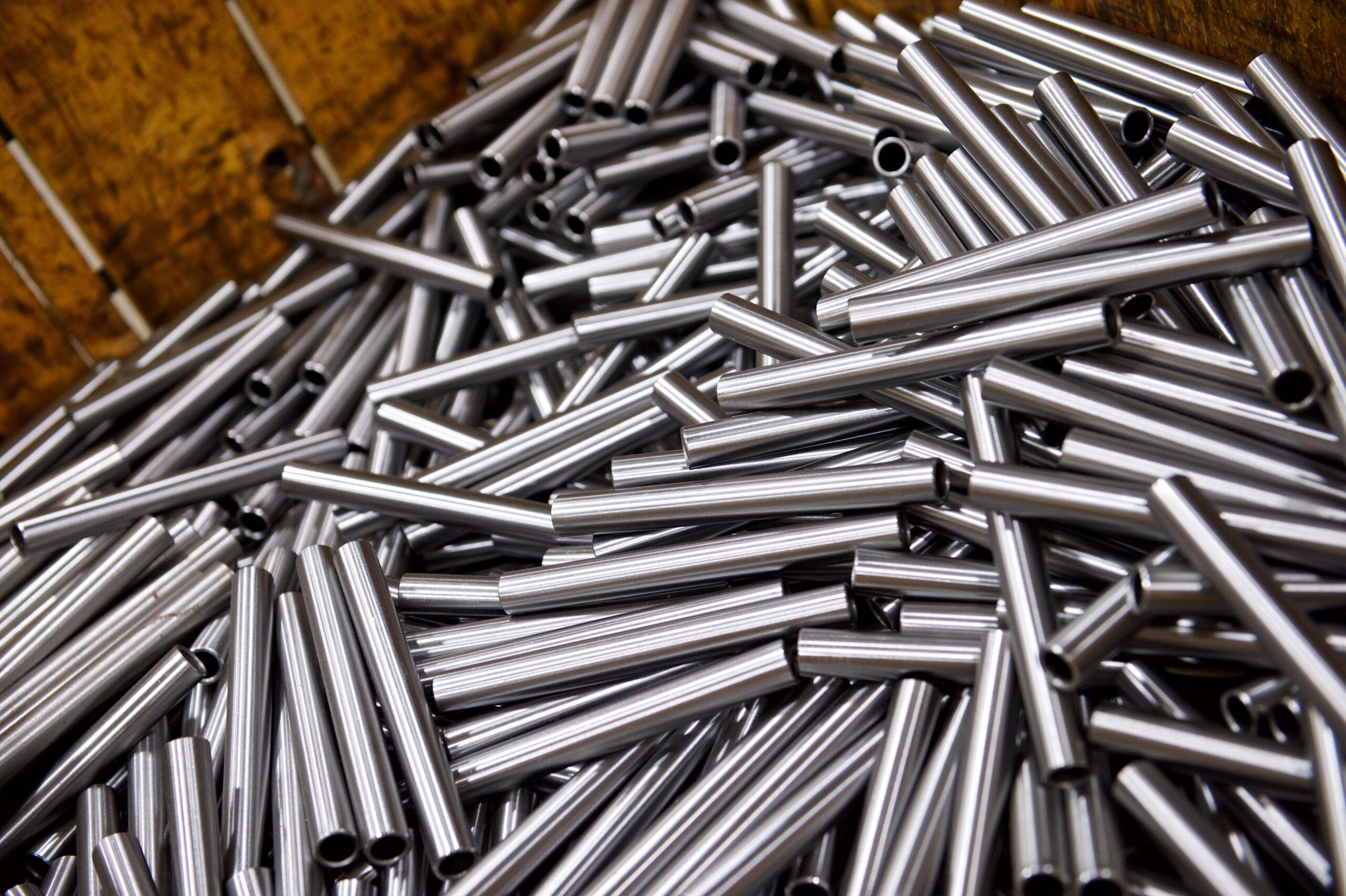
Stainless Steel vs. Aluminum Tubing: Which Should You Choose?
Manufacturing professionals often face critical decisions when selecting materials, such as stainless steel or aluminum tubing. Each material has unique properties that make it more suitable for different applications. Choosing the wrong type of steel tube could impact your project’s longevity, performance, and cost-effectiveness. Ultimately, selecting the appropriate material for use comes down to several factors.
Strength and Durability: How Much Toughness Do You Need?
Stainless Steel Tubing
Stainless steel is known for its exceptional strength and high resistance to bending, warping, and wear, making it ideal for high-stress applications. Whether working with high-pressure systems, heavy-duty construction, or industrial machinery, stainless steel’s durability makes it a solid choice for long-term, demanding use.
Aluminum Tubing
While lighter and softer than stainless steel, aluminum tubing offers a surprising amount of strength in non-structural applications. It holds up well under moderate stress but is less resilient in high-impact environments. Aluminum is an excellent choice when weight reduction is more important than extreme durability.
Bottom Line: For applications involving heavy loads or high stress, stainless steel tubing is the safer choice. Aluminum works best in less demanding roles, particularly when minimizing weight is a priority. Using aluminum in a high-stress setting could lead to bending or structural failure, resulting in costly repairs and downtime.
Weight: Does Every Ounce Count?
Stainless Steel Tubing
Due to its higher density, stainless steel is heavier than aluminum. The added weight can benefit applications requiring stability but may be a disadvantage if lightweight construction is preferred.
Aluminum Tubing
Aluminum’s lightweight nature is one of its greatest advantages. Aluminum tubing weighs about one-third as much as stainless steel and is commonly used in the automotive and aerospace industries, where reducing weight is necessary for efficiency and performance.
Bottom Line: If weight reduction is essential to your project, aluminum tubing is likely the best choice. If weight is less critical, stainless steel’s added heft provides valuable structural stability.
Malleability: Need Complex Shapes or Custom Bends?
Stainless Steel Tubing
Stainless steel is durable but less malleable, making it challenging to shape and bend. Bending stainless steel tubing requires specialized equipment, which can add to production costs, especially for intricate designs.
Aluminum Tubing
Aluminum’s lower density and unique malleability make it ideal for complex shapes and custom designs. This flexibility makes aluminum tubing a popular choice for products that require specific bends, such as HVAC systems, automotive frames, and architectural fixtures.
Bottom Line: Aluminum tubing is better suited for projects with complex or custom shapes. Stainless steel can work for these projects, but the added effort may only be worth it if enhanced durability is required.
Corrosion and Moisture Resistance: Can Your Tubes Handle Tough and Wet Environments?
Stainless Steel Tubing
Stainless steel’s outstanding corrosion resistance is attributed to its protective chromium oxide layer, which helps prevent rust and degradation. It is particularly effective for harsh environments—outdoor settings with constant weather exposure or industries where tubes may come in contact with chemicals, including alkaline or acidic substances. Additionally, stainless steel maintains its integrity in high-humidity and submerged conditions, such as marine and industrial applications, where high moisture exposure and durability are essential.
Aluminum Tubing
Aluminum also resists corrosion due to its oxide layer, which forms when exposed to air. However, aluminum’s resistance is generally lower than that of stainless steel in highly acidic, alkaline, or saltwater conditions. It performs adequately in environments with mild humidity or controlled moisture levels but may deteriorate more quickly than stainless steel in aggressive conditions. For applications where aluminum must withstand frequent moisture contact—like indoor settings with some humidity or outdoor use in non-marine areas—anodizing can enhance its corrosion resistance and prevent pitting.
Bottom Line: Stainless steel is a better choice for high-exposure, high-moisture, and chemical-heavy environments where long-term durability is essential. Anodized aluminum can serve well in controlled indoor conditions or milder outdoor applications with less moisture exposure.
Heat Resistance: Are Your Tubes Taking on High Temperatures?
Stainless Steel Tubing
With a melting point above 2,500°F, stainless steel maintains strength and integrity under extreme heat. It is ideal for applications like exhaust systems, boilers, and other high-temperature environments.
Aluminum Tubing
While aluminum functions well at moderate temperatures, it can lose structural integrity in high-heat settings. Aluminum’s melting point is around 1,200°F, which may start to soften at temperatures exceeding 400°F, depending on the application.
Bottom Line: Stainless steel tubing is the better choice for products exposed to high temperatures. Aluminum is more suited for environments with controlled or lower temperatures.
Talk to the Steel Experts
With years of experience supplying high-quality stainless steel and aluminum tubing, our experts can help by evaluating your project’s demands and recommending the best tubing material to meet your needs.
In addition to our extensive inventory, Westfield Steel offers value-adding custom fabrication services to ensure your tubing arrives cut to spec, bent to fit, and ready for installation. With our reliable logistics through Westfield Steel Express, you can trust that your order will arrive on time and to your specifications.
Ready to get started? Contact our steel experts today for a personalized consultation and quote.
Back