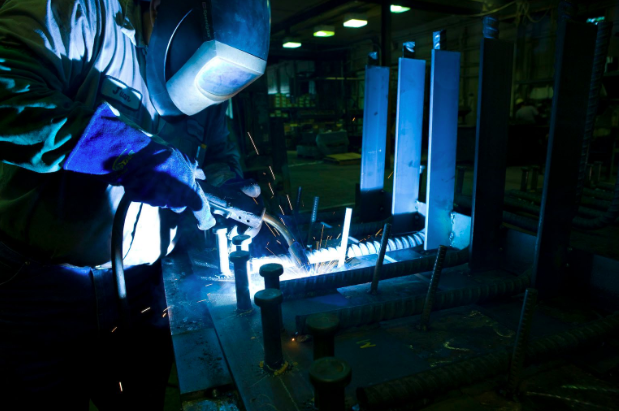
Welding Steel with MIG or TIG Welding & the Best Welding Metals
Welding steel is both a science and an art. Just as scientists and artists use various tools and supplies to achieve their desired outcomes, so do experienced and versatile welders. Depending on the properties, sizes and applications of the metals used, welding steel can be done in many ways. That said, MIG welding and TIG welding have become two of the most popular processes in metal fabrication. This post takes a closer look at these two common and capable methods for welding steel, their key differences and unique advantages, and the traits that determine which metals can be welded most effectively.
What is MIG Welding?
MIG (metal inert gas) welding, also known as GMAW (gas metal arc welding), is a type of arc welding widely utilized in products spanning many industries. In arc welding, an electric arc is created between a consumable or non-consumable electrode and the base material to melt and join metals with high heat.
MIG welding uses an automatic arc with a thin consumable wire electrode as the filler material and a shielding gas mixture of argon and carbon dioxide to protect the weld. The electrode wire acts as a glue in MIG welding, which is common with steel, stainless steel, and aluminum for applications in the construction, manufacturing, and automotive industries, among others.
What is TIG Welding?
TIG (tungsten arc gas) welding, or GTAW (gas tungsten arc welding), also uses an arc process. But its electrode is non-consumable tungsten and used alongside a separate and manually fed filler material. The shielding gas to protect the weld in TIG welding is typically 100 percent argon. Carbon dioxide promotes tungsten oxide formation that could wear down an electrode prematurely or contaminate a weld.
TIG welding can weld steel, aluminum, and other metals with high levels of precision typically required in industrial structure manufacturing, the aerospace industry, motorsports, and more. Its strength also lends TIG welding to withstanding water pressure in pipeline welding or other secure construction uses.
These two common types of welding steel and other metals share several similarities, including using electric arcs and shielding gases, but their differences provide a number of advantages and disadvantages across various applications.
When to Use MIG Welding or TIG Welding
Generally, thicker and heavy-duty welds utilize MIG welding, while thinner metals require the TIG welding process.
One advantage of MIG welding is that it’s faster than TIG welding, creating shorter production lead times and lower costs. While TIG welding will have longer production times and higher costs, TIG welds are stronger, more precise, and more aesthetically pleasing than MIG welds.
Welders can take steps to increase the strength of MIG welds, but TIG welding’s narrow and focused arc makes for better penetration as it melds the metal together. The faster speed of MIG welding comes due to its automatic-feed filler material and a rounder, broader arc that can better dissipate heat than TIG welding torches. TIG welding produces little to no splatter, usually only requiring light polishing and producing work typically viewed as the best weld aesthetics available. MIG welds will often be suitable in applications where welds will later be covered, coated, or hidden out of sight.
If your project or application calls for a thicker metal supply or high productivity, MIG welding will be best. The continuous wire feed will require stopping and starting to replace filler material less regularly than with TIG welding, resulting in a decreased chance of weld defects.
However, TIG welding is best suited for shorter runs, especially in applications with thinner materials that could be burned or warped without the high precision and accuracy of the TIG welding process.
Which metals can be welded?
While generally all metals can be welded, some are not ideal, and the materials’ various properties must be considered regarding the type of welding used.
Low-carbon mild steel is widely regarded as one of the most weldable metals. Thanks in part to long-term high demand across many applications, industry advancements have historically prioritized improvements to power sources, filler material compositions, and more for welding low-carbon steel.
Due to having very small amounts of carbon (0.1-0.3 percent) and only trace amounts of other alloying elements, low-carbon steel can be deformed without fracturing and is much more malleable than other types of steel. Steels with more carbon content are prone to cracking, while a carbon amount below 0.12 percent can cause microscopic holes in the metal.
Provided there are no other impurities in the metal, low-carbon steels can be welded using MIG, TIG, or any other welding process type.
Common everyday applications for low-carbon steel include many construction and bridge parts, plumbing pipes, and beverage cans.
Medium-carbon (0.3-0.6 percent) and high-carbon (0.6-1 percent) steels possess increased strength but are much more susceptible to cracking and, therefore, more difficult to weld. Specialty low-hydrogen welding processes and fillers are necessary for welding these steels.
The automobile industry utilizes medium-carbon steels extensively in making gears, axles, shafts, couplings, and more. Possessing extreme strength and hardness, high-carbon steels are commonly used in making masonry and cutting tools.
When it comes to working with non-steel metals, TIG welding was first popularized for joining aluminum and has played a big role in the industry’s acceptance of the metal in high-quality welding.
Welding steel to aluminum presents some unique challenges in reactions between the compounds, but it is possible and routinely done on steel pipeline or ship deck components. Covering the steel in a dip coating can help it act more like aluminum, and TIG welding will give a much more reliable and higher-quality weld than MIG welding when melding two different metals.
Certain stainless steels are well-suited for MIG and TIG welding practices. However, their complex chemical composition will cause any attempted welding between stainless steel and aluminum to be brittle and easily break under slight pressure. TIG welding stainless steel to mild steel is possible, but the MIG process is much preferred when welding stainless steel with dissimilar metals. The process will require the right selection of filler material with properties equal to or greater than the lesser of the two materials being welded together for best effects.
Welding at Westfield Steel
Westfield Steel’s welding capabilities are vast, versatile, and held to the highest quality standards. Proudly certified by the American Welding Society and Canadian Welding Bureau. Westfield Steel is also ISO 9001:2015 certified in recognition of quality management systems and consistent precision in producing products that meet customer and regulatory requirements.
Westfield Steel ensures all our customers receive production-ready steel welding in products that are safe and tested to the highest quality standards. First founded in 1977 as a family-owned company with a deeply rooted midwestern history, Westfield Steel has grown and evolved to encompass not just welding, assembly, and steel fabrication but also light manufacturing and a dedicated distribution arm, Westfield Steel Express.
Back