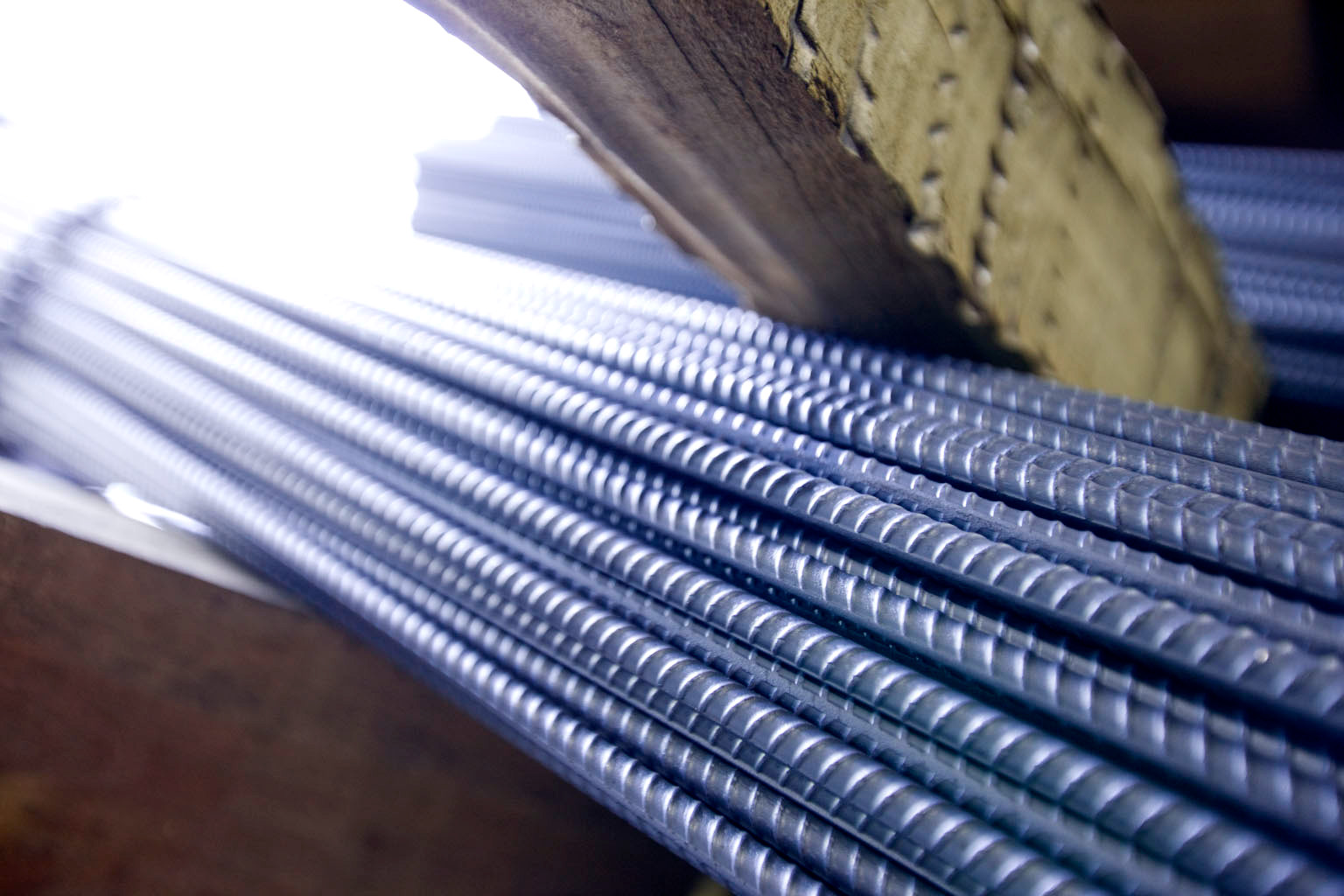
The Hidden Costs of Low-Quality Steel Bars for Construction: How to Spot Inferior Materials
Cutting corners on material quality may lower upfront costs—but it can lead to far more expensive consequences. From structural failure to costly rework and legal liability, low-quality steel bars pose hidden risks that few construction teams can afford to overlook. Sourcing from a reputable steel supplier and knowing how to spot inferior materials is essential to avoid these setbacks.
Market Growth Raises the Stakes for Steel Bar Quality
As demand for steel bars in construction continues to rise—projected to reach $3.9 billion globally by 2030—the pressure to source materials quickly and affordably has never been greater. But with that demand comes increased risk: substandard products can more easily enter the supply chain when quality oversight is rushed or overlooked. In this environment, working with a trusted steel supplier becomes even more critical to protect your project’s timeline, budget, and long-term structural performance.
Visual Red Flags: Identifying Defects in Steel Bars
Inferior steel bars for construction can exhibit several physical defects that compromise structural integrity. Regular inspections and adherence to stringent quality control processes are imperative to detect and address defects before they impact construction projects. Being vigilant about these defects can prevent future complications.
Surface Cracks or Pitting
Surface cracking and pitting defects often result from poor casting practices or using substandard raw materials. Surface cracks may appear as visible lines or fissures while pitting manifests as small, localized depressions or holes on the steel surface. Both can act as stress concentrators, leading to premature failure under load.
Dimensional Inconsistency
Variations in the thickness or diameter of steel bars can lead to uneven load distribution within a structure. For example, a beam able to accommodate a specific bar diameter may experience unexpected stress if the bars are undersized, potentially causing deformation or collapse.
Rust or Oxidation
The presence of rust indicates exposure to moisture and inadequate protective measures during storage or transportation. Rust can reduce the cross-sectional area of the steel bar, diminishing its load-bearing capacity. Early signs include discoloration, flaking, or a rough surface texture.
Unlabeled or Mislabeled Bars
Proper identification markings are essential for traceability and verification of compliance with industry standards. Bars lacking clear labels or those with inconsistent markings may not meet specified mechanical properties, posing a risk to structural performance.
Fabrication Failures: Common Welding Issues That Undermine Quality
Even high-quality steel bars can become ineffective if met with poor fabrication and welding practices. Substandard workmanship can lead to structural weaknesses and increased maintenance costs. Keep a close eye out for indicators of inferior fabrication.
Porosity or Cracking in Welds
Porosity refers to small cavities or holes within the weld metal, often caused by trapped gases during solidification. Cracks may develop due to rapid cooling or excessive stress. Both defects compromise the strength and continuity of the weld, making the joint susceptible to failure.
Inconsistent Bead Profiles
A weld bead should have a uniform width and height, indicating consistent heat input and travel speed during welding. Irregular bead profiles, such as excessive convexity or concavity, suggest poor technique and can lead to weak joints.
Lack of Fusion at Joints
A lack of fusion occurs when the weld metal fails to properly fuse with the base metal or preceding weld passes. You will likely notice visible gaps or a lack of penetration at the weld interface, resulting in reduced load-bearing capacity.
Misaligned or Warped Assemblies
Improper fixturing or heat distortion during welding can lead to improperly aligned components. This misalignment can cause uneven load distribution and difficulties during assembly or installation.
What to Look for in a Reliable Steel Supplier
A reputable steel supplier will provide full traceability, up-to-date mill test reports, and verified compliance with ASTM standards. In addition to maintaining ISO 9001 certification and offering transparent documentation on quality control procedures, a dependable supplier will also employ American Welding Society (AWS) Certified Welding Inspectors (CWIs). CWIs are trained to detect weld defects, identify inadequate practices, and enforce strict compliance with welding codes and industry standards. These combined credentials demonstrate a supplier’s commitment to excellence and significantly reduce risk throughout every phase of your construction project.
The Westfield Steel Advantage: Steel Bars for Construction with Confidence
Westfield Steel has been a trusted provider of high-quality construction steel bar products and fabrication services for over four decades. Our comprehensive and certified services include precision cutting, drilling, bending, welding, and more, tailored to meet the unique demands of your projects. Our experienced team collaborates closely with clients to deliver custom solutions that align with project specifications and timelines. Do not compromise on quality. Contact Westfield Steel today to consult with our experts and receive a personalized quote for steel bars that meet the highest standards of excellence.
Back